6 ways to save energy when you’re moving water with a pumping system
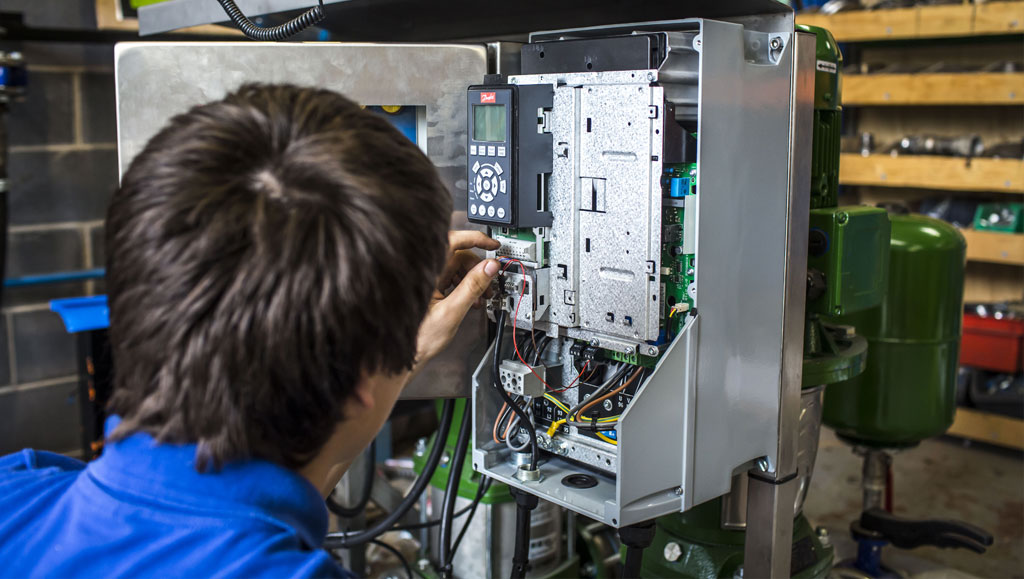
Pump stations are required when water needs to be pumped from a low level up to a higher one to flow into a water system. They work by increasing pressure and forcing water through the resistance in its path. They’re vital pieces of equipment for distributing clean water and removing wastewater, along with having numerous functions in industry.
All this takes energy. In a world where we’re increasingly aware of energy efficiency, all businesses are conscious of their responsibilities. An inescapable fact is that pumps contribute significantly to a carbon footprint:
- Pumps account for up to 10% of the world’s energy consumption
- 60% of pumps use up to 60% more energy than they should
- High efficiency pumps could reduce global electricity consumption by 4%
Here are 6 ways to save energy and reduce your pump’s carbon footprint:
1. Choose the most efficient pump for the application
The design stage of pump development often results in oversizing. This is due to the practice of adding multiple safety factors, and can be a result of the manufacturer failing to tailor a pump to its optimal level. In addition to size, pumps need to be carefully selected and designed to take into account the power and speed requirements, along with the type of drive, mechanical seal, and other ancillary equipment.
2. Minimise the pressure drop in the system
Optimising your pipe system is as crucial as optimising your pump. A drop in system pressure can be affected by factors such as flow rate, pipe size, length and characteristics, and the type of fluid being pumped. Manufacturers will optimise your pipes as part of a complete pumping solution.
3. Use control valves effectively
Flow and/or pressure is controlled by control valves within a pumping station. Energy losses are prevented with valves by their capacity to throttle and bypass flow. This keeps flow at its optimal level and doesn’t waste energy.
4. Choose the best pump seals
Sealing systems, including static and dynamic seals, have an impact on pump efficiency. They lose energy through mechanical friction, in addition to the energy leaks between the pump suction and pump discharge units. There are significant energy savings to be made from choosing proper pump seals with a record in high efficiency.
5. Maintain the pump properly
In a piece of machinery with moving parts and high quantities of fluid passing through, the need for regular maintenance is paramount to continued effectiveness. An engineer will be able to identify problem areas from their inspection, including common issues such as rotor erosion. Preventative and predictive maintenance can minimise any drop in efficiency caused by these problems.
6. Eliminate any unnecessary uses
This is where utilising the services of experienced pump designers and manufacturers can improve your carbon footprint. They will be able to ensure that there are efficiency measures are built into your system, including shutting down unnecessary pumps when flow requirements alter.